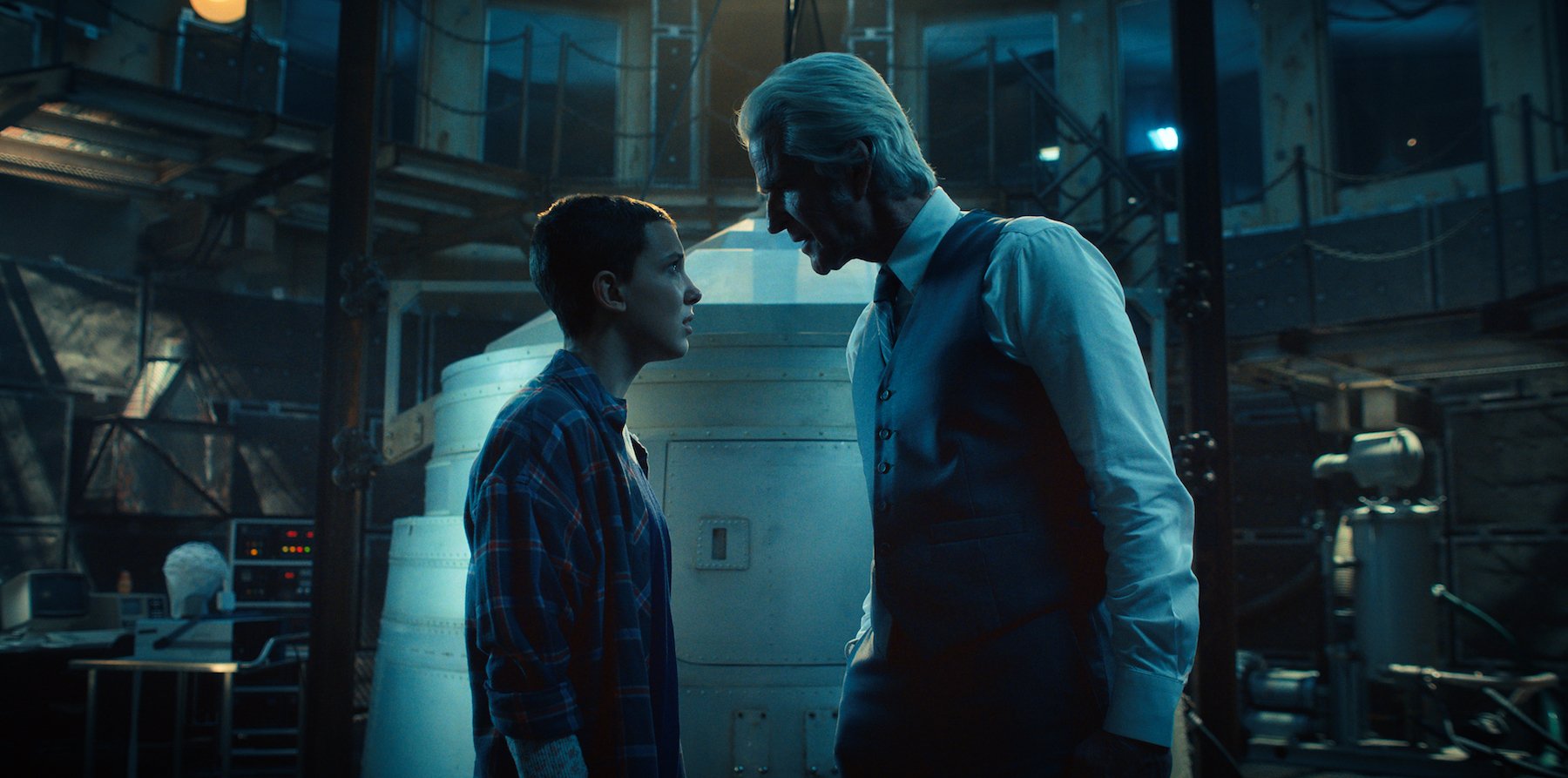
Three Characters Died in ‘Stranger Things 4’ Volume 2 Instead of the Rumored Five
Now that Stranger Things 4 Volume 2 is out there, many fans have questions about the characters who die in new episodes. After hearing rumors that there would be five deaths in Volume 2, most fans only counted three. Here’s who died in Stranger Things 4 Volume 2 compared to who fans thought would die, plus the one fan with a questionable fate.
[SPOILER ALERT: Spoilers ahead for Stranger Things 4 Volume 2.]
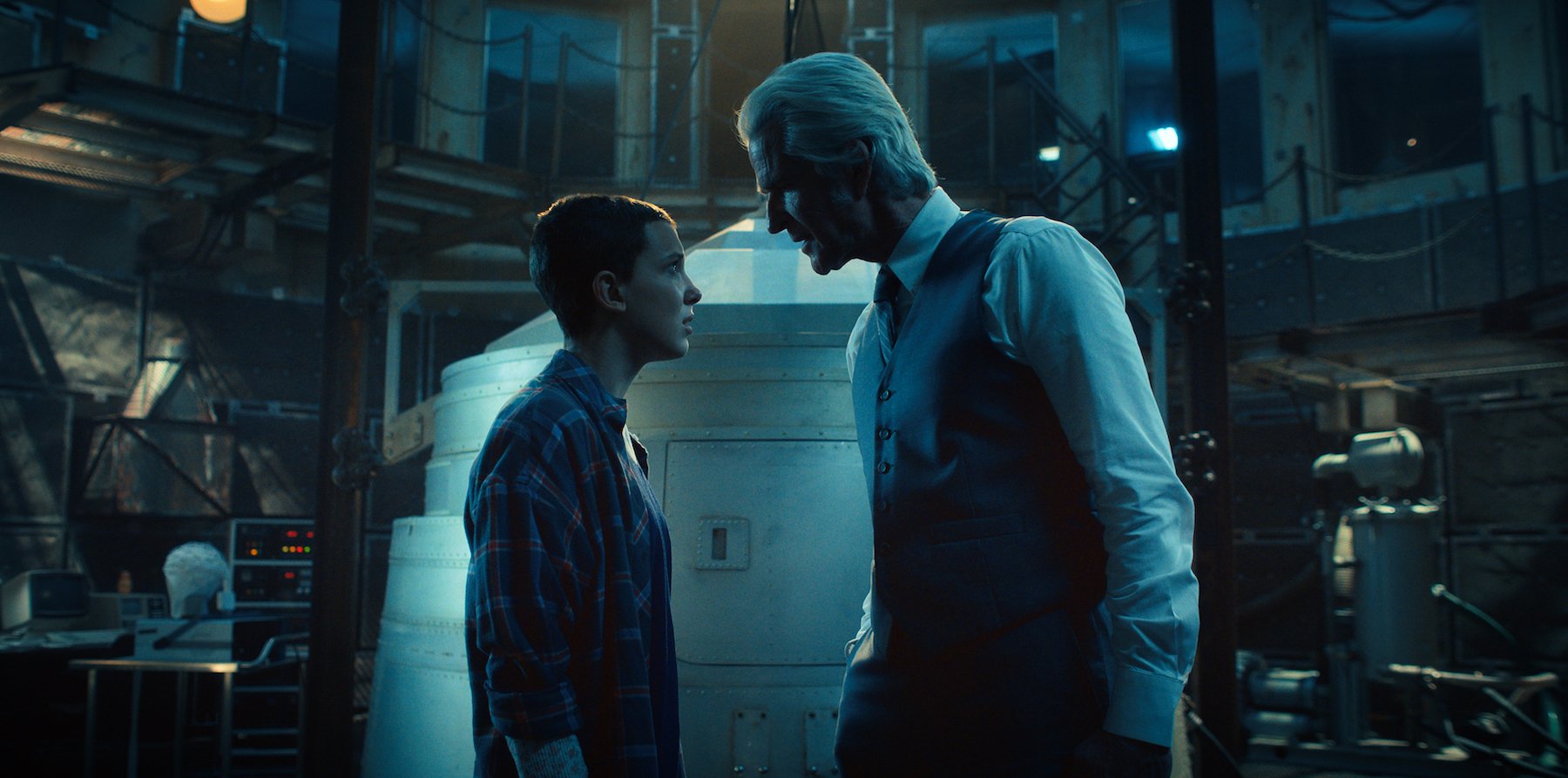
Fans heard rumors about five characters dying in ‘Stranger Things 4’
In an interview with Variety ahead of the final two episodes, Ross Duffer said fans should be “concerned” about characters going into Volume 2. However, he never specified how many characters. More specifically, Duffer said: “I don’t really want to say, but I would be concerned about the characters going into Volume 2, for sure.”
It didn’t take long for Stranger Things fans on Reddit to spin this into the “five confirmed deaths” you’ve probably heard of. “I heard a rumor that 5 named characters are going to die this season (don’t know how accurate that is) so I’m basing my kill count off of that,” said one Redditor.
They thought Dr. Owens, Argyle, Mrs. Wheeler, Robin or Nancy, and Yuri would die in Volume 2. Now that we’ve had a chance to digest the last two episodes of Stranger Things 4, we know all of those characters are safe. We use that term loosely, because who knows how safe Dr. Owens (Paul Reiser) really is.
Who dies in ‘Stranger Things 4’ Volume 2?
Three main characters die in Stranger Things 4 Volume 2: Dr. Martin Brenner (Matthew Modine), Eddie Munson (Joseph Quinn), and Jason Carver (Mason Dye). In “Chapter 8: Papa,” a military sniper in a helicopter shoots Brenner down as he tries to escape the Nina Project’s secret location with Eleven (Millie Bobby Brown).
Eddie meets his demise in “Chapter 9: The Piggyback.” Regardless of how prepared fans felt — especially after seeing the teaser for Volume 2 — Eddie’s death hit many fans the hardest. After his and Dustin’s (Gaten Matarazzo) plan to distract the demobats with an epic version of Metallica’s “Master of Puppets” goes sideways, Eddie opts to give Dustin more time to escape. In the end, after “not running away this time,” Eddie dies in Dustin’s arms in one of the most emotional moments from Volume 2.
In the final moments of “The Piggyback,” Jason inserts himself in the middle of Lucas (Caleb McLaughlin) and Max’s (Sadie Sink) plot to destroy Vecna (Jamie Campbell Bower). Believing Lucas is part of Eddie’s satanic cult, the two get into a fight. Eventually, Lucas knocks Jason out, leaving his body directly on top of the gate that splits through Hawkins in the episode’s final moments, leaving his body to turn to Upside Down dust.
Does Max die in ‘Stranger Things’?
Max volunteers herself as bait in Stranger Things 4 Volume 2. While Max distracts Vecna, Steve (Joe Keery), Nancy (Natalia Dyer), and Robin (Maya Hawke) torch Vecna’s recharging body with Molotov cocktails. However, when Jason arrives in the attic of the Creel house, he distracts Lucas from pulling Max out of Vecna’s Curse. Her bones start to break and her eyes start to bleed, leaving many fans wondering if Max lives or dies.
Max isn’t dead at the end of Stranger Things 4. However, she is in a coma and in the hospital with several broken bones. Moreover, she lost her vision. While it’s unlikely, Max could die in Stranger Things Season 5. But we’ll have to wait a few years until we find out.
Watch Stranger Things on Netflix.