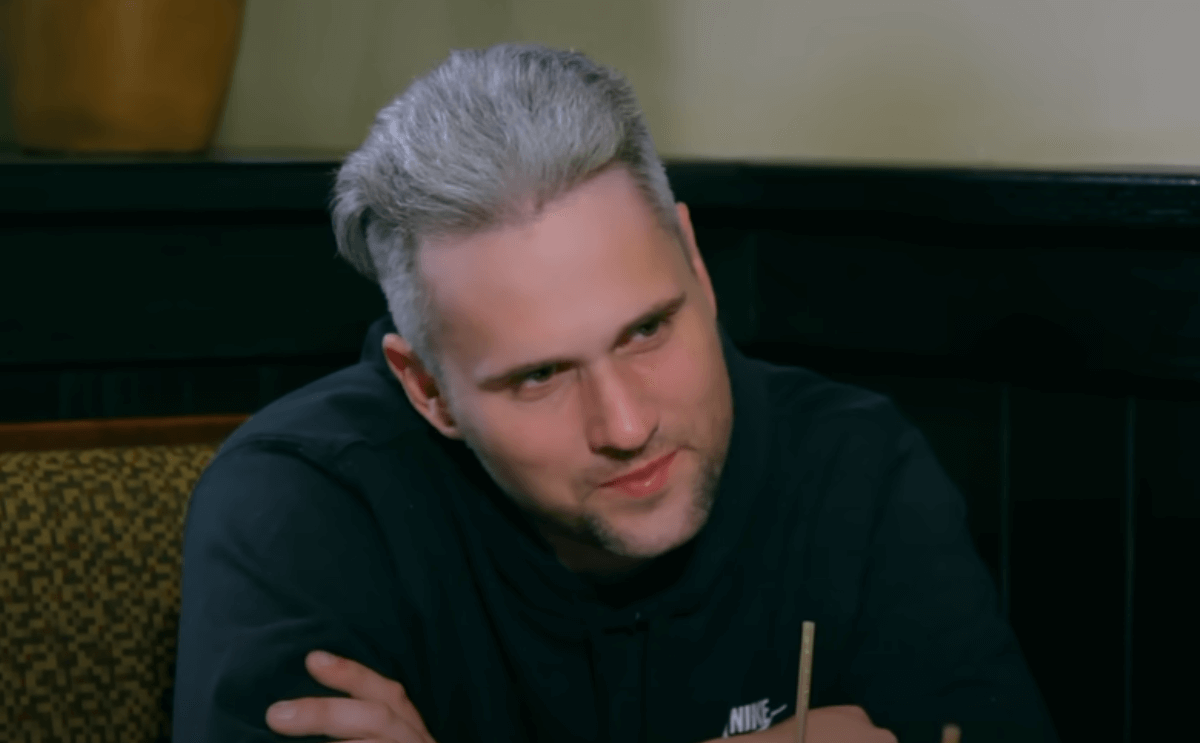
‘Teen Mom’ Star Ryan Edwards Ordered to Pay Child Support Just as He Welcomes New Baby
Ryan Edwards’ life has been moving fast for the last two years. The troubled reality TV star has found himself in trouble with the law, pushed into a court-ordered rehab, and back on reality TV all in 24 months. He’s also announced a divorce, an engagement, and a new baby in the same timeframe.
While it has been a wild ride for the Teen Mom: The Next Chapter star so far, things are getting more complicated. A judge recently ordered Edwards to pay child support to his soon-to-be-ex, and now he’s welcomed a new baby.
Ryan Edwards ordered to pay child support
Ryan Edwards and Mackenzie Standifer have faced off in court yet again. While the couple’s divorce is not yet final, a judge has finally gotten around to ruling on child support. According to court documents, Edwards has officially been ordered to pay Standifer $1,553 per month for the two children they share.

The judgment isn’t the final call on child support, though. According to the Ashley Reality Roundup Group, the monthly amount could change based on later testimony. An additional court date will likely take place to figure out back child support and how much back support he will owe the mother of his two children.
If Edwards is on the hook for back support, he’ll likely have to fork over a large sum of money all at once. Edwards and Standifer separated two years ago. According to Standifer, he has never paid child support, meaning he could be 24 months in arrears. Edwards has not commented on the child support ruling, but he did announce the birth of his fourth child.
Ryan Edwards and Amanda Conner welcome their first child together
While Ryan Edwards and Mackenzie Standifer were busy facing off in court over the two kids they share, Edwards was celebrating the arrival of yet another youngster. Edwards’ fiancee, Amanda Conner, gave birth to their first child together.
The couple announced the arrival via People. They told the publication Presley Sage Elianna Edwards was born on Feb. 12 at 6:15 am. The baby girl is Conner’s second child. Conner has chronicled her custody battle for her oldest child on TikTok. A judge granted her custody in late 2024.
The new arrival is Edwards’ fourth child. He welcomed his first son, Bentley Edwards, with his high school girlfriend, Maci Bookout, in 2008. He also shares a son, Jagger Edwards, and a daughter, Stella Edwards, with soon-to-be-ex-wife Mackenzie Standifer.