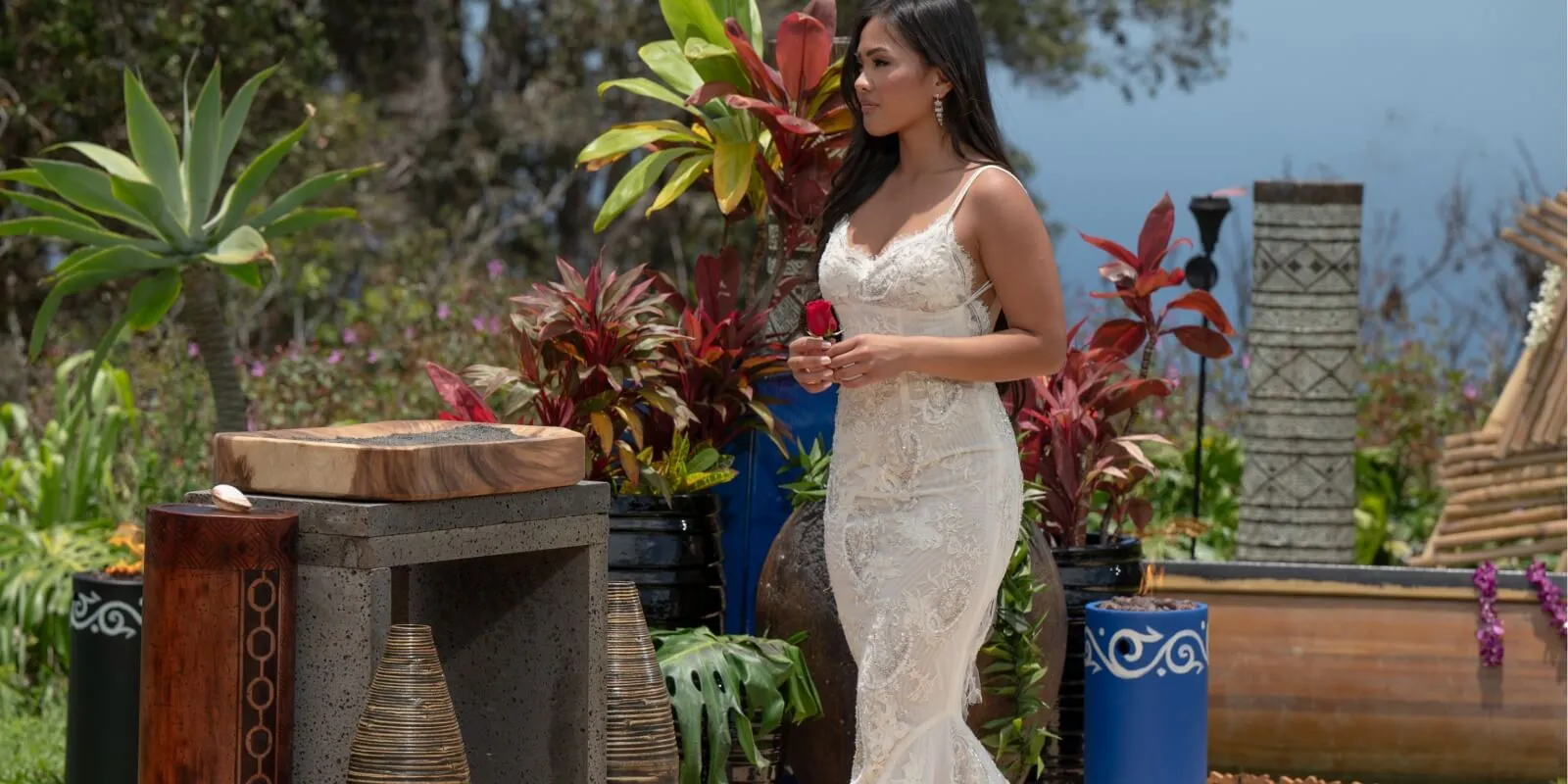
Can ‘The Bachelorette’ Survive Its 2025 Hiatus? Exposing the Cracks in the ABC Franchise
The Bachelorette will not air a new season in the summer of 2025. The series will return in the future, but it’s unlikely to debut in a new installment this year. Has production reassessed the competition dating series and realized its flaws? Here’s what needs to change so the series survives and thrives in the future.
Did Jenn Tran’s season expose the cracks in ‘The Bachelorette’?
The Bachelorette was always second cousin to The Bachelor, ABC’s original dating series. This is evident by the sheer number of seasons (28) of the original male-helmed franchise to the female-led series (21).
The Bachelorette leads are typically chosen from the group of finalists on the previous season of The Bachelor. Producers generally select the female contestant with the most fan support as its lead.
Season 21 of The Bachelorette appeared to have issues from the start. Both Daisy Kent and Maria Georgas revealed they had turned down the opportunity to lead the franchise. This made lead Jenn Tran’s casting mishandled from the start.
Tran never had a chance to thrive as the Bachelorette. Production interference throughout the season, including the surprise arrival of Tran’s ex-Matt Rossi, and what seemed to be an extra amount of manufactured drama for ratings between contestants left a sour taste in viewers’ mouths.
Tran and Devin Strader became engaged during The Bachelorette finale. However, viewers later learned Strader ended their relationship shortly after proposing.
Deadline reported on Feb. 7 that The Bachelorette was paused for its summer 2025 season. The last three seasons of the series typically began production during the winter and aired mid-summer.
Has ‘The Bachelorette’ paused production before?
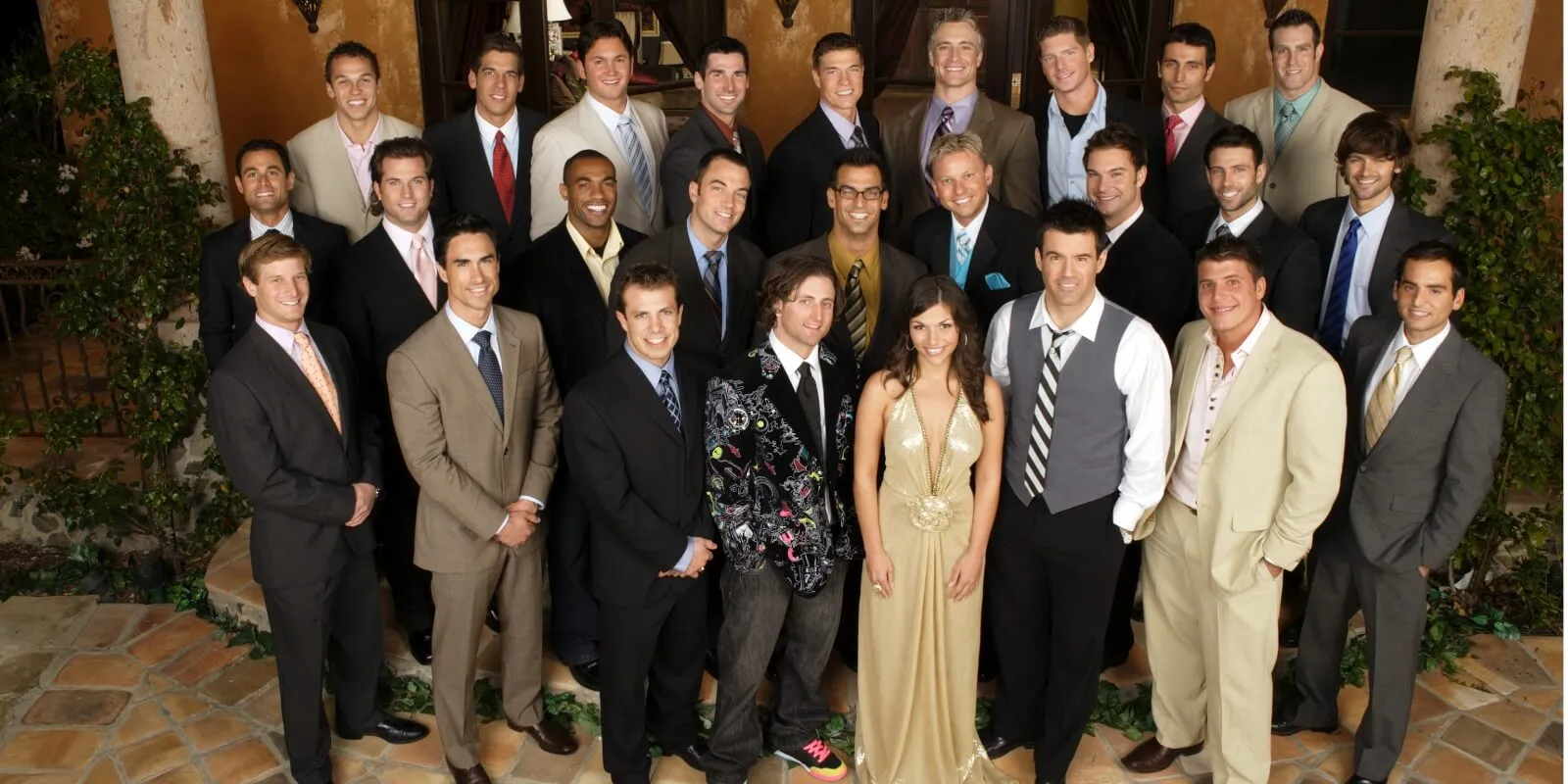
Longtime Bachelorette viewers have been through this type of production hiatus before. The show took breaks in 2006 and 2007 before returning in 2008 with season 4.
In 2021, The Bachelorette aired two seasons. Katie Thurston and Michelle Young led back-to-back installments plagued with filming delays and scheduling conflicts caused by the coronavirus (COVID-19) pandemic and Young’s role as a teacher.
Young was runner-up to Rachael Kirkconnell in Matt James’ Bachelor season. In season 25, James broke up with Kirkconnell after her past racially insensitive social media posts were exposed. The couple reunited in April 2021 but broke up for good in January 2025.
Only three couples who became engaged during 21 seasons of The Bachelorette remain married today. The couples who found their happily ever after include Trista Rehn and Ryan Sutter of season 1, season 9 stars Desiree and Chris Siegfried, and JoJo and Jordan Rodgers of season 20.
What is Jenn Tran doing now?
The day after The Bachelorette finale ended, Jenn Tran was hired as Dancing with the Stars last contestant for season 33. She was paired with pro Sasha Farber, who was also a last-minute add.
The couple’s chemistry was evident. Although they landed in seventh place for their season, Tran and Farber appear to have personally connected. According to recent reports, the couple live together in Farber’s California home.
Until a decision is made regarding a new season of The Bachelorette, fans of the franchise can whet their appetites with a new season of The Bachelor, featuring Grant Ellis (from Tran’s season) currently airing on Mondays at 8 p.m. ET on ABC.
Season 10 of Bachelor in Paradise premieres in 2025. The exact premiere date has not been announced yet.