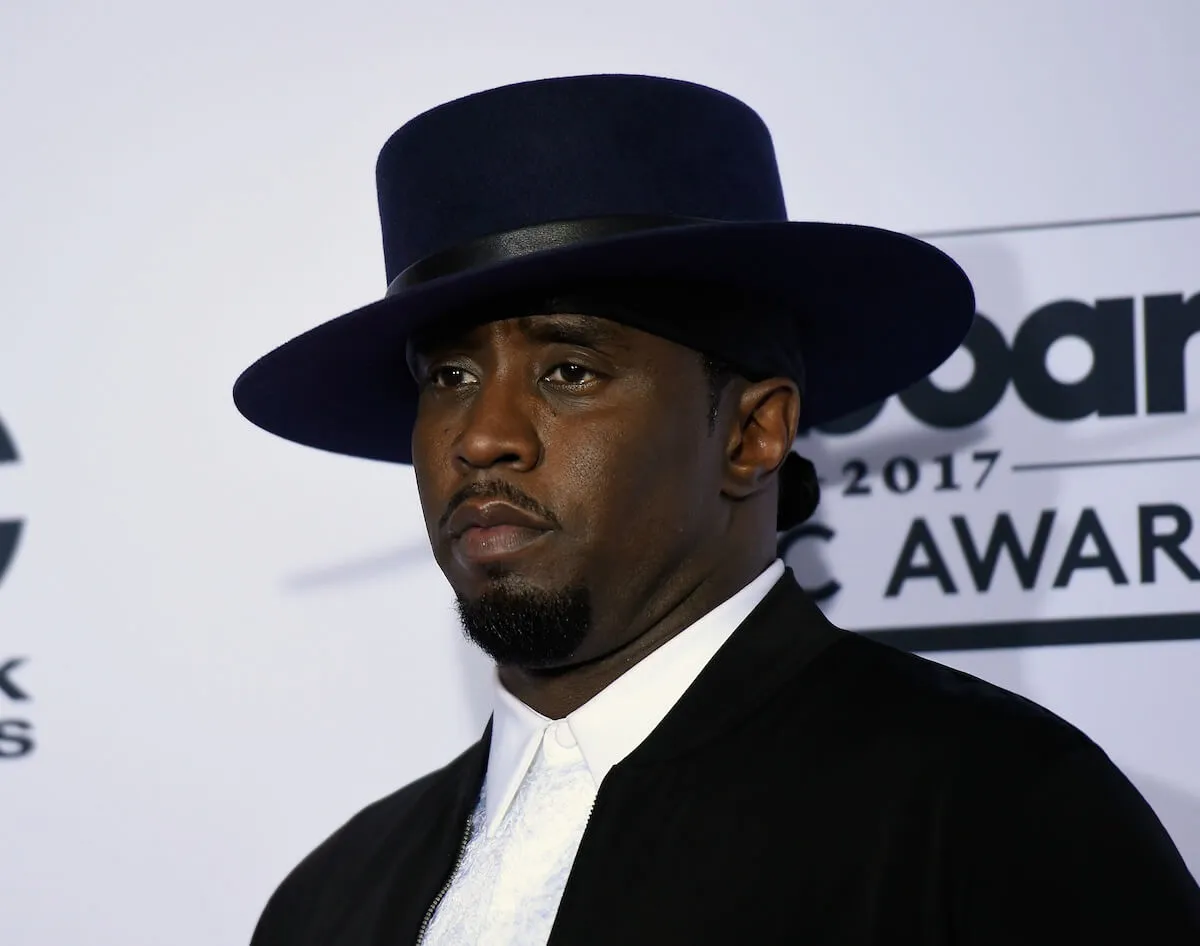
Featured Stories
One Member of Diddy’s Legal Team Quits Case With Ominous Statement: Who Are His Remaining Lawyers?
Sean 'Diddy' Combs' is set to stand trial this spring, but his defense team just had a major shakeup. Anthony Ricco has quit. He still has a team behind thim, though.